私も含めて「何度も尻を叩いてもらった」お陰で活動が進みました!
小林興業 株式会社
代表取締役 : 小林 智 様
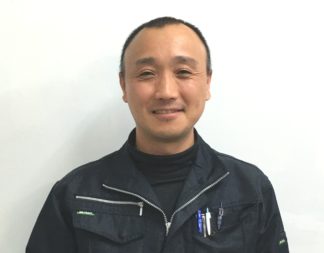
Q:どんなきっかけで5Sに取組もうと考えたのですか?
当社は、主にカメラ関連の精密部品を加工しています。年間で1,500~2,000種類の製品を作っていますが、各製品毎に異なる加工工具や治具を使うことが多く、また試作開発を数多くおこなうため、社内がモノで溢れていました。
長年、何とかしたいなぁと思い、よさそうな方法を探していたところ「5S」に関する本を見つけ、読んだのがきっかけです。
Q:当社に依頼された経緯を教えてください。
工場が広く対象物も多いため、社員を巻き込む必要がありました。本は読んだものの、5S活動の経験がないため、実際に何から手を付けてよいか分かりませんでした。そこで、会計事務所に相談したところ、5S活動の指導実績が豊富な会社があるということで紹介してもらいました。
Q:依頼するにあたり不安はありませんでしたか?
依頼前に、まず工場全体を見てもらい幾つかアドバイスをもらいました。そのアドバイスがどれも的を射ていました。
また、他社の事例を写真で見せてもらったり、実際の進め方を提案書で具体的に示して貰えたので、任せても大丈夫だと感じ、お願いしました。
Q:実際は、どんな形で活動を進めたのですか?
当社では30名ほどの中核社員に参加してもらい、8ヶ月にわたり 月1回のペースで指導を受けました。具体的な指導内容は全体を前半/後半の2部に分け、前半が5Sの考え方や活動のポイントに関する講義と、これまでの活動中に生じた諸問題に対するアドバイス、後半が各職場の巡回指導というかたちで進められました。
また、研修と次回研修までの間は、全社一斉の5S活動の時間を毎週1時間設けました。活動中に生じた疑問やうまくいかない点は纏めておいて、次回訪問してもらった時にアドバイスを受けて解消していきました。
Q:工場の中は、どんな変化がありましたか?
とくかく何度もしつこく言われたのが「使えるか/使えないか」ではなく、「使うか/使わないか」で判断してください。ということです。会社の中にあるモノは全てお金がかかっているので、使えるモノってなかなか捨てられないんですよね。
でも、何度も指導を受けたお陰で、会社全体で3割程度のモノが減りました。6畳程度の広さの開発品置き場なんかは、8割ほど減容できました。
Q:その他に、何か変化はありましたか?
8ヶ月の活動を通して、社員の意識が変わってきたのは感じていましたが、最後に「清掃の頻度」を決めた時にハッキリと確信しました。
これまでは、トイレは当番制で清掃していたものの、各職場の清掃というのは、個々の社員や職場毎に気になった時と年末にやるぐらいで、会社としては決めていませんでした。このため、さすがに「毎日清掃をやろう」と言ったら反発するだろうと思い、「週2回やる事」を提案しました。ところが、何人かの社員がどうせやるなら「毎日やった方がいい」と言ってくれて、皆もそれに賛同してくれたんですね。この時は、本当に嬉しかったです。
Q:最後に、依頼してみてどうでしたか?
平田さんの指導を受けたことで、会社の中がスッキリして広くなりました。また、当社の実態を踏まえて活動を定着させるための仕組みもアドバイスしてもらえました。頼んでよかった思うのは、躓いたときに的確にアドバイスを貰えた点と、私も含めて「何度も尻を叩いてもらった」お陰で活動が進んだ点です。私一人では、短期間にここまで進めるのは難しかったと思います。
ご感想有難うございました。